The new Bob Marshman building at the Construction Training Centre (CTC) is an exciting new recently completed training centre building. Our clients at CTC wanted to create a living laboratory that explores emergent passive thermal design principles and sustainability and the impacts of these on construction education pathways. The building itself provides new training areas in a prominent yet underutilised part of their campus at Salisbury.
CTC were keen to test and design alternative sustainability approaches and to subsequently measure the effectiveness of the outcomes through ongoing monitoring of the building. The CTC Campus at Salisbury was originally the steel fabrication facility for the Story Bridge, dating back to 1935. Since 1994, CTC has established the site as a state of the art training community, providing future skills and knowledge required for the construction industry. The site now includes a mixture of teaching spaces at a range of scales from classroom environments through to interactive industrial spaces.
The significant scale and presence of the existing industrial buildings on site strongly influenced the building form and the coarseness of its articulation. Internally, the building contrasts this with soft, warm, and engaging finishes and materials that support a range of teaching and collaboration activities plus user well-being.
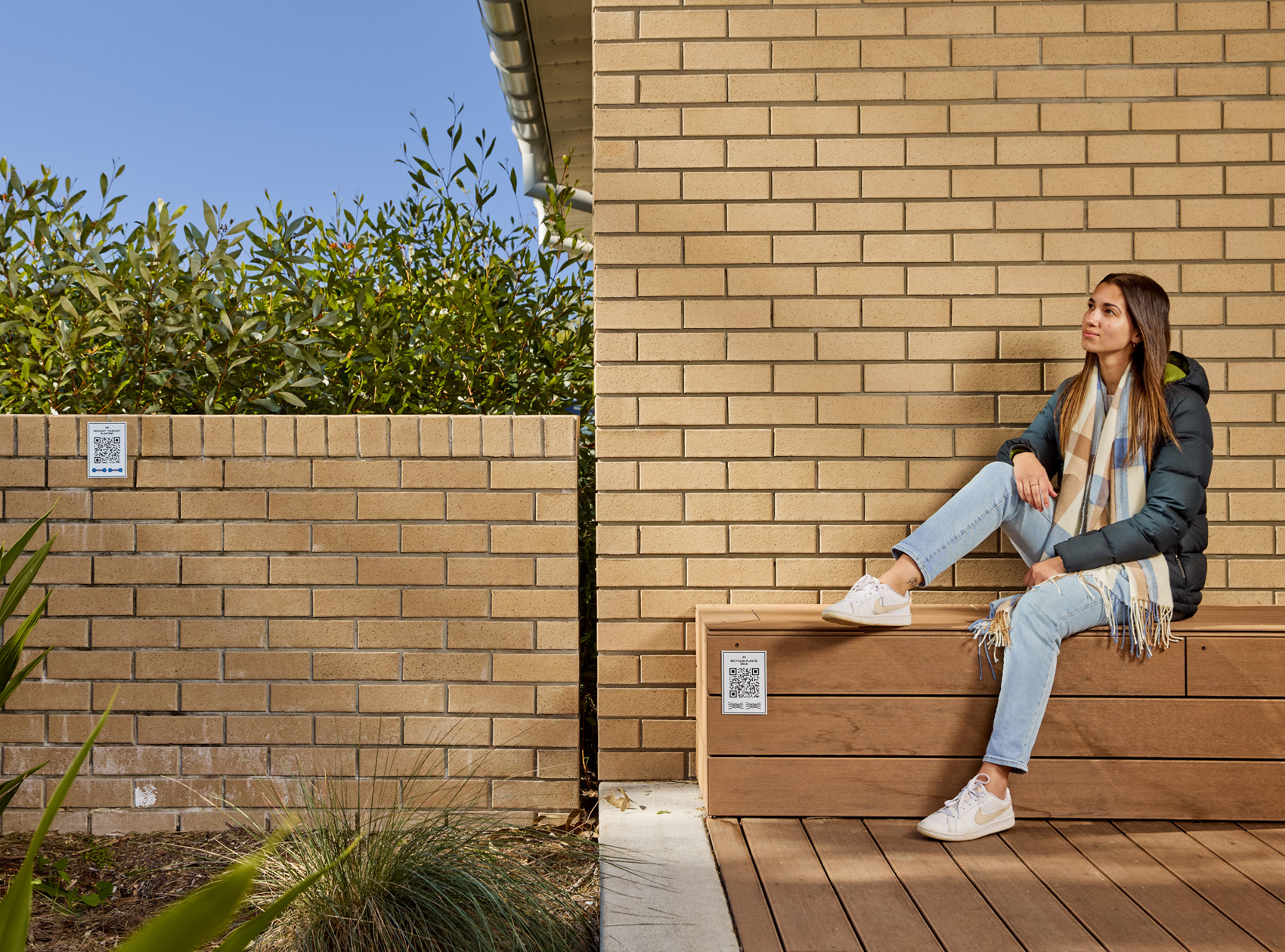
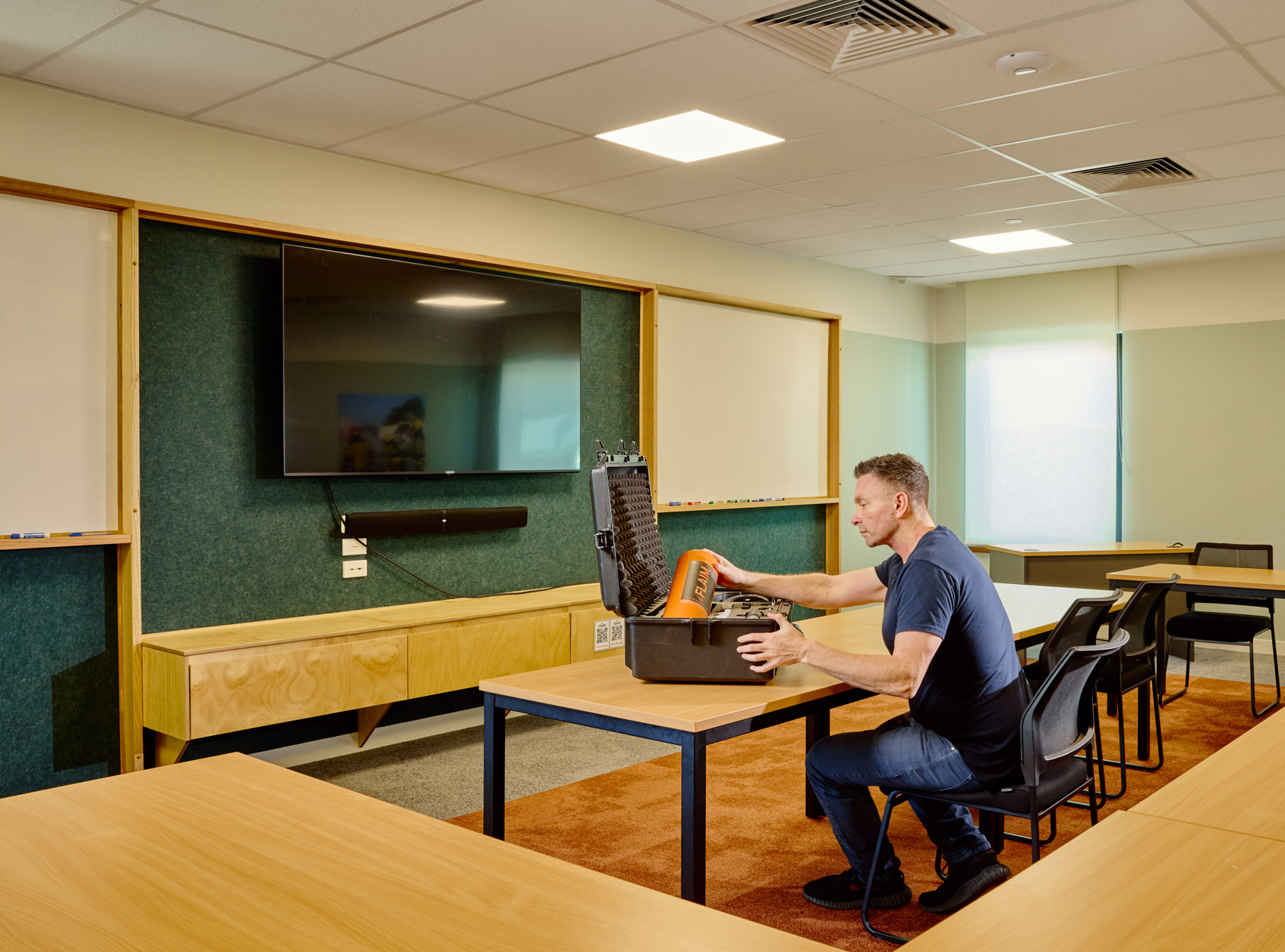
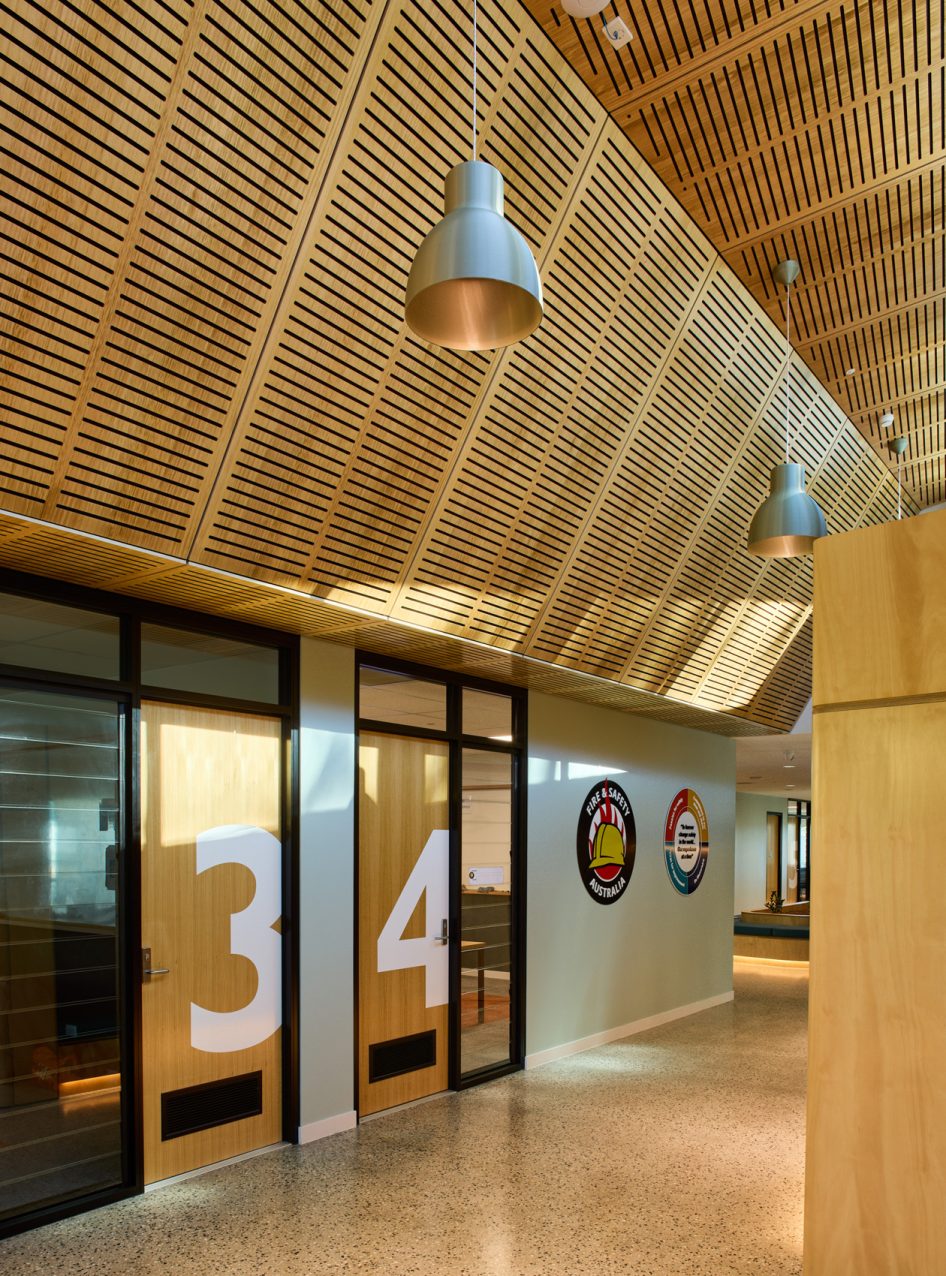
The nature of education is that teaching spaces need to be able to adapt quickly to the needs of changing technologies and emerging occupations. The building planning adopts a cruciform circulation pattern and a loose fit structural grid to enable easy reconfiguration throughout the life of the building.
CTC is a self-funded entity, so all projects need to be able to demonstrate tangible benefits that do not unduly compromise the financial performance of the organisation. The cost benefits of traditional design as opposed to Passiv Haus were carefully analysed through detailed design and ongoing operational costs. While there was a small cost impact of adopting Passiv Haus, the long-term modelling demonstrated a significant saving in overall cost of operation.
Passiv Haus certification requires an extremely air tight building with significant amounts of thermal insulation. This approach reduces the cooling energy required. However, with such a large number of occupants, the mechanical systems needed to adapt in order to maintain air quality and humidity to support high information uptake. Close collaboration between Eco Latteral, BEC, and DR was essential to overcome this.
We are excited to see the quantitative results of taking this design approach.
A life cycle analysis undertaken by WSP found a 24% reduction in carbon emissions compared to a traditional building approach. CTC has committed to monitoring the energy use and performance of the completed building, which we will consider in our post occupancy evaluation of the project in 2025.
The strong sustainability objectives influenced all material and construction methodologies.
The emphasis was placed on Australian made, locally manufactured, robust, and easy to maintain materials with lower embodied carbon. Circularity was stressed through the use of materials with high recycled content and opportunities for end-of-lifecycle reuse and recycle. Some examples of the rigorous material selection process included bricks with recycled content from Cross River Rail sites made in Brisbane, SEQ grown and locally processed hoop pine for plywood joinery, kitchen benchtop made by Five Mile Radius from concrete and aggregate salvaged from construction sites, and Australian made recyclable carpet tiles and post-consumer PET recycled pinboards.
- Client
Construction Training Centre
- Year
2024
- Location
Salisbury
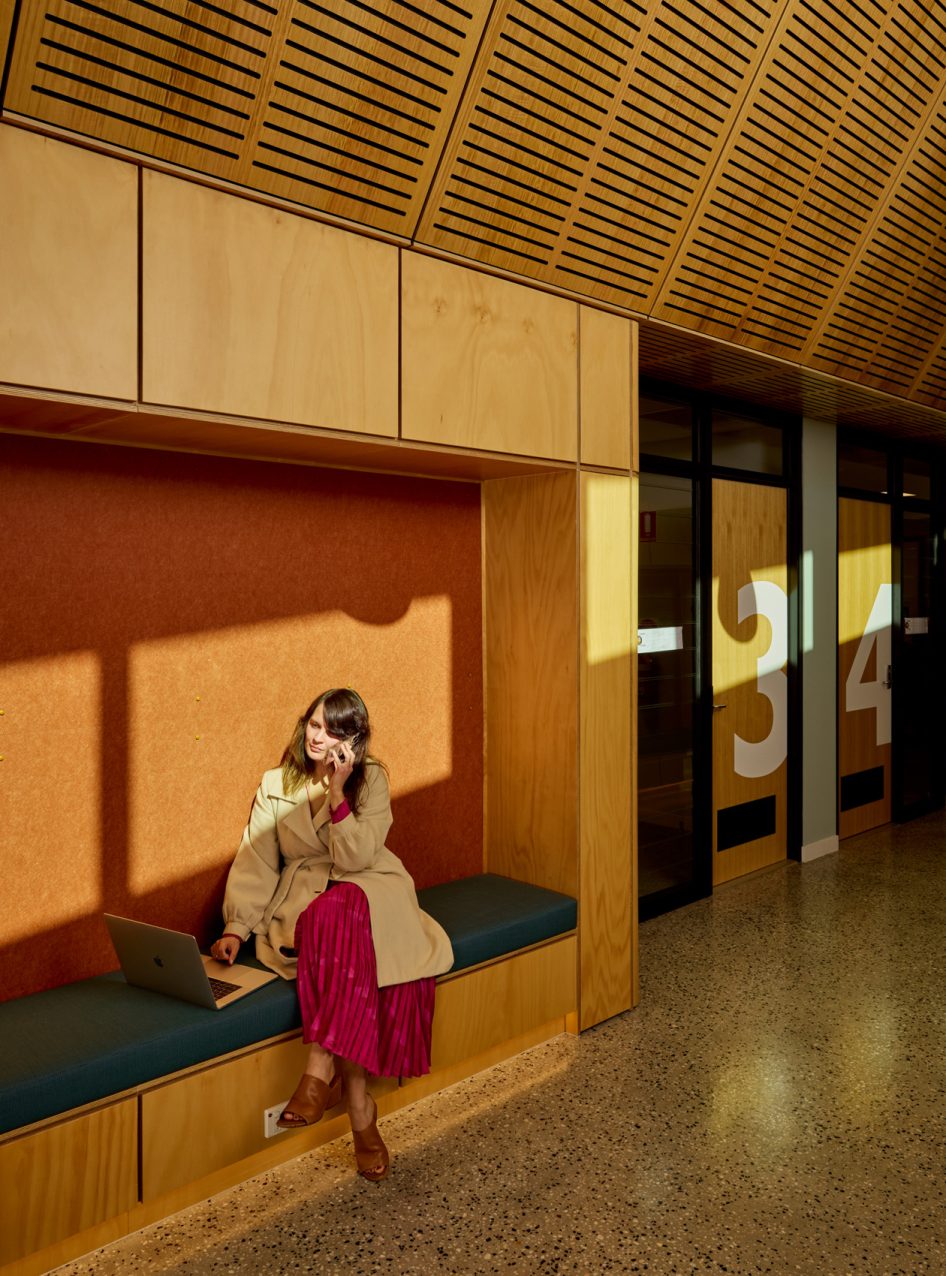
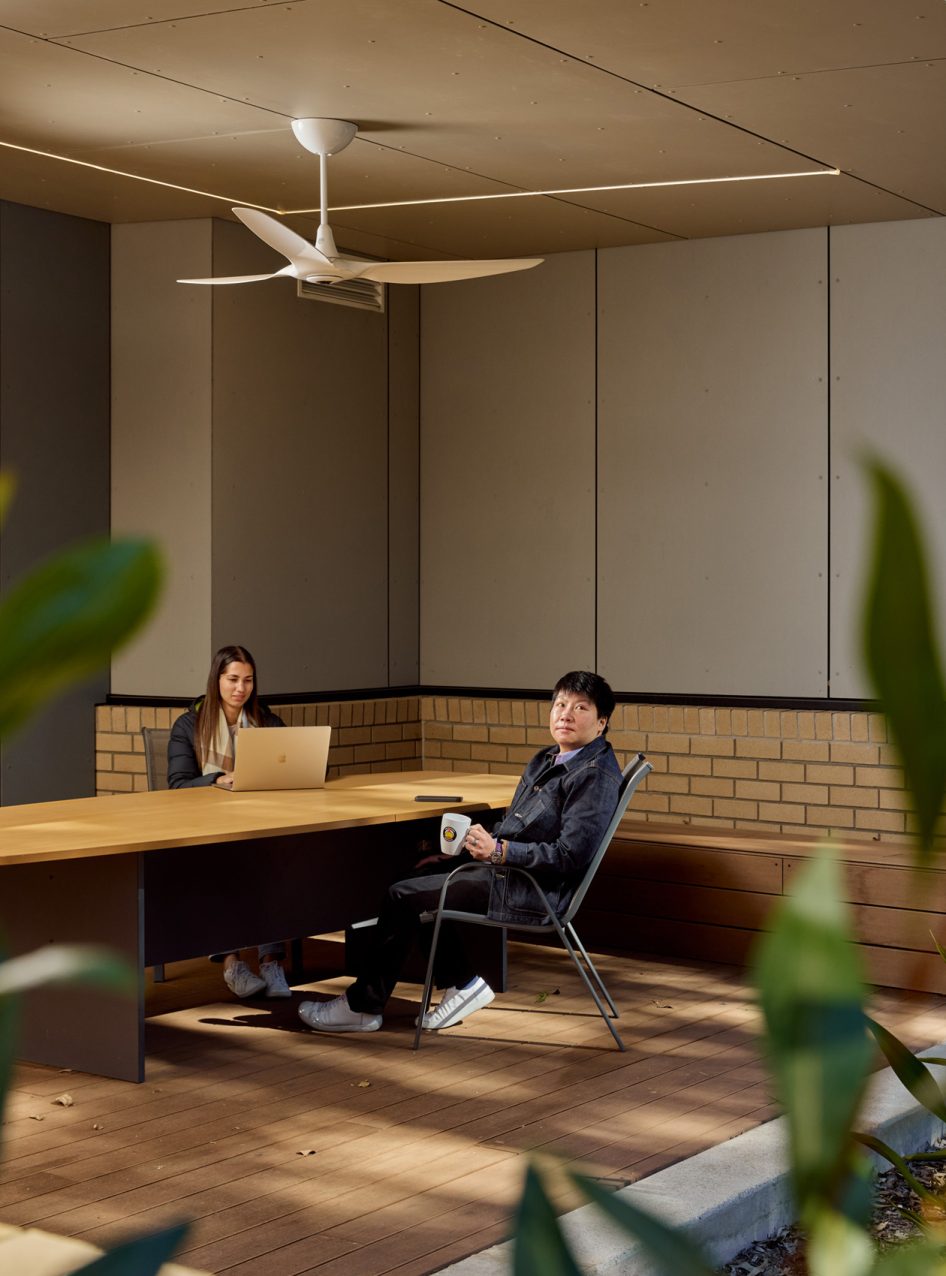